CNC Fräsen
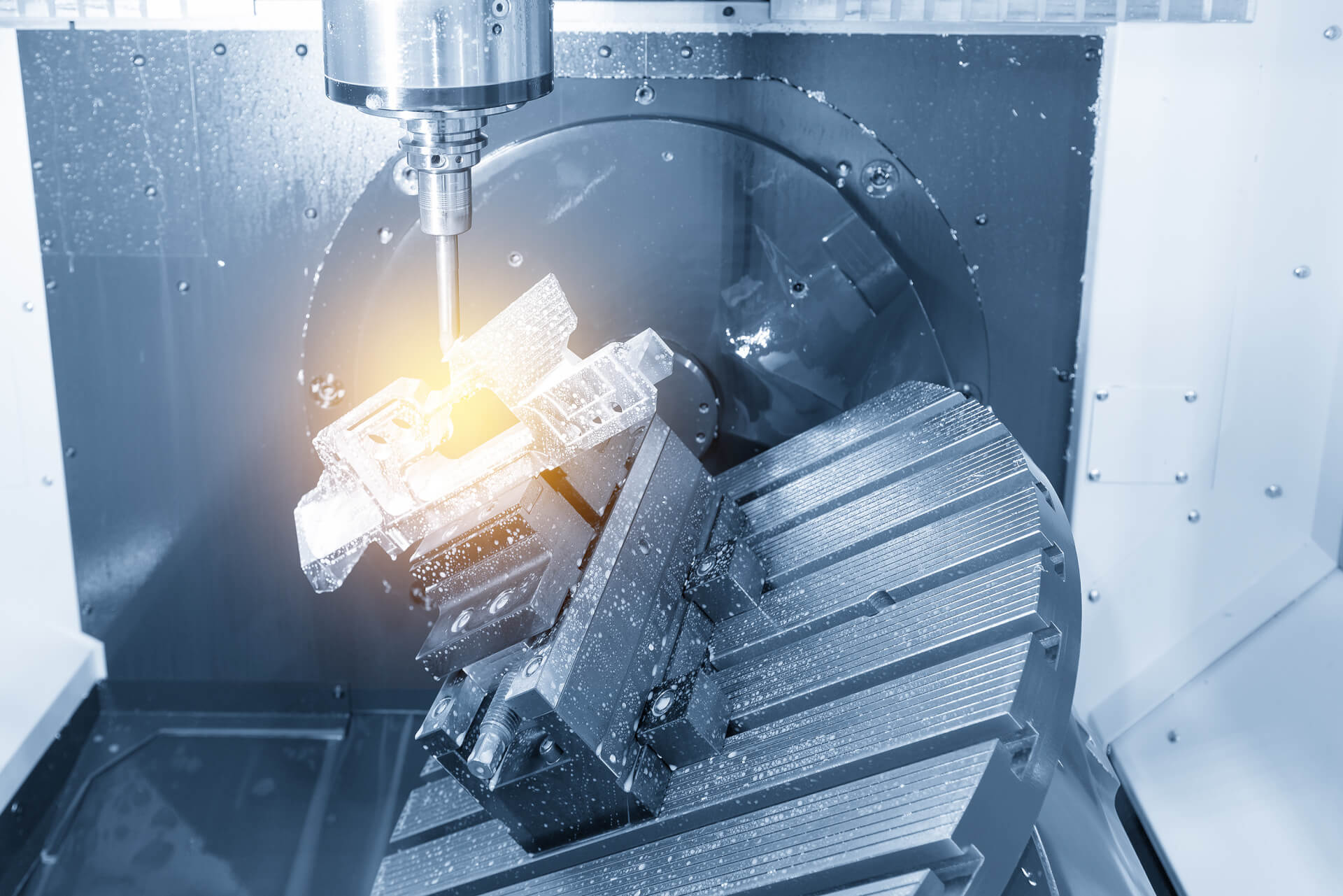
1. Grundlagen und Einführung
Was ist CNC-Fräsen?
CNC-Fräsen (Computerized Numerical Control) ist ein sehr genaues Verfahren zur Fertigung. Dabei wird Material von einem Werkstück abgetragen, um die gewünschte Form zu erhalten.
Die Geschichte des Fräsens ist alt. Der große Sprung kam aber in den 1940er Jahren mit der Numerischen Steuerung (NC). Sie wurde für die Flugzeugindustrie entwickelt. Damals steuerten Lochkarten und Magnetbänder die Maschinen.
In den 1970er Jahren folgte die Revolution zur Computerized Numerical Control (CNC). Nun übernahmen kleine Computer, sogenannte Mikroprozessoren, die Steuerung. Das brachte viele Vorteile:
- Viel höhere Genauigkeit
- Mehr Anpassungsfähigkeit
- Weitgehende Automatisierung
Das Grundprinzip ist geblieben: Ein rotierendes Werkzeug nimmt Material vom Werkstück weg. Dies geschieht nach präzisen Anweisungen des Computers. Moderne CNC-Fräsmaschinen sind heute technische Meisterwerke. Sie können komplexe Formen sehr genau herstellen.
Technische Grundlagen des CNC-Fräsens
Die Steuerungssysteme sind das Herz jeder CNC-Maschine. Sie übersetzen die Befehle aus CAD/CAM-Programmen (Computer-Aided Design / Computer-Aided Manufacturing) in exakte Achsenbewegungen.
Maschinen gibt es mit vielen Achsen:
- 3-Achs-Maschinen: Bewegen sich in X-, Y- und Z-Richtung. Gut für einfache Teile.
- 5-Achs- oder 5+2-Achs-Maschinen: Können Werkstück oder Fräskopf zusätzlich drehen und schwenken. So lassen sich Teile von allen Seiten in einem Arbeitsgang bearbeiten. Das spart Zeit und macht es genauer.
Es gibt auch verschiedene Steuerungsarten:
- Punktsteuerung: Hier werden nur die Endpunkte der Bewegung festgelegt.
- Bahnsteuerung: Ermöglicht eine durchgehende Bewegung entlang einer vorgegebenen Linie. Das ist wichtig, um komplizierte Formen zu fräsen.
CAD/CAM-Software ist unerlässlich. Sie hilft, komplexe Zeichnungen direkt in Maschinencodes umzuwandeln.
Varianten und Fräsarten
Beim CNC-Fräsen gibt es zwei Hauptarten des Fräsens, jede mit eigenen Vor- und Nachteilen:
- Gegenlauffräsen:
- Das Werkzeug bewegt sich entgegen der Richtung, in die sich das Werkstück bewegt.
- Vorteile: Das Werkzeug zieht sich weniger leicht ins Material, manchmal bessere Oberfläche bei rauen Materialien.
- Nachteile: Höherer Werkzeugverschleiß, die Kräfte drücken gegen den Vorschub (kann Vibrationen verstärken).
- Gleichlauffräsen:
- Werkzeug und Werkstück bewegen sich in dieselbe Richtung.
- Vorteile: Weniger Kräfte, bessere Wärmeabfuhr, längere Lebensdauer des Werkzeugs, oft bessere Oberflächen.
- Dies ist heute in der modernen Fertigung oft die bevorzugte Methode.
Welche Fräsmethode die beste ist, hängt stark vom Material, der gewünschten Oberfläche und der Stabilität der Maschine ab.
2. Technologien und Maschinen
Moderne CNC-Maschinen & Automatisierung
Moderne CNC-Bearbeitungszentren sind heute sehr komplexe Systeme. Sie können viel mehr als nur fräsen. Oft vereinen sie auch Drehen, Bohren und Schleifen in einer Maschine.
Automatisierung ist hier der Schlüssel zu Effizienz und Wirtschaftlichkeit. Dazu gehören:
- Automatische Werkzeugwechsler: Sie haben Platz für viele Werkzeuge und tauschen diese sehr schnell aus.
- Palettenwechselsysteme: Während ein Werkstück bearbeitet wird, kann schon das nächste vorbereitet werden. Das nutzt die Maschinenlaufzeit optimal.
- Integrierte Qualitätskontrollsysteme: Messtaster oder Sensoren prüfen die Maße direkt in der Maschine und korrigieren bei Bedarf die Werkzeugposition.
Diese Automatisierung ermöglicht oft den Betrieb ohne ständige menschliche Aufsicht. Das steigert die Produktivität deutlich und senkt die Personalkosten.
Nachrüstbarkeit & Technische Details
Manchmal können auch ältere Maschinen auf die CNC-Technologie aufgerüstet werden. Das ist oft günstiger als eine ganz neue Maschine zu kaufen. Es ist zwar technisch aufwendig, kann aber die Lebensdauer und Leistung alter Anlagen stark verbessern.
Wichtige technische Details sind:
- Antriebssysteme: Servomotoren oder Schrittmotoren setzen die Computerbefehle in präzise Bewegungen um.
- Wegmesssysteme: Glasmaßstäbe oder Sensoren messen die genaue Position der Achsen. Sie geben diese Information an die Steuerung zurück.
Nur durch diese ständige Kontrolle können CNC-Maschinen so genau arbeiten. Die Qualität dieser Bauteile ist entscheidend für die Leistung der Maschine.
SPS als Bindeglied zwischen Steuerung und Maschine
Die Speicherprogrammierbare Steuerung (SPS) ist ein wichtiges, aber oft übersehenes Bauteil. Sie verbindet die CNC-Steuerung mit den physischen Teilen der Maschine.
Die CNC-Steuerung berechnet die komplexen Bewegungen des Werkzeugs. Die SPS hingegen kümmert sich um die Zusatzfunktionen. Dazu gehören:
- Die genaue Steuerung der Kühlmittelzufuhr.
- Die nötige Schmierung der Maschinenteile.
- Die Überwachung von Sicherheitsfunktionen (z.B. Schutztüren).
- Die Steuerung von Werkzeugwechslern oder Spannvorrichtungen.
Die SPS sorgt dafür, dass alles reibungslos läuft und die Maschine sicher und effektiv arbeitet. Sie überwacht die Maschine ständig und reagiert auf Probleme. Ohne eine gut programmierte SPS wäre der vollautomatische Betrieb moderner CNC-Maschinen nicht möglich.
3. Materialien & Werkstoffe
Materialvielfalt beim CNC-Fräsen
Das CNC-Fräsen ist sehr vielseitig. Man kann damit eine große Auswahl an Materialien bearbeiten.
Bei Metallen sind das zum Beispiel:
- Aluminium: Leicht und gut zu bearbeiten.
- Edelstahl: Rostfrei und robust.
- Titan: Sehr fest und leicht, auch für Medizintechnik geeignet.
- Messing: Leitet Strom gut und lässt sich leicht bearbeiten.
- Verschiedene Speziallegierungen für besondere Anforderungen.
Neben Metallen werden auch viele Kunststoffe wie POM, PEEK, ABS oder PVC gefräst. Sie kommen in der Medizintechnik oder bei Konsumgütern zum Einsatz. Auch Holz für Modelle oder Formen, sowie innovative Materialien wie Keramik oder Verbundwerkstoffe können präzise bearbeitet werden. Diese Vielfalt ermöglicht die Herstellung von Produkten für unterschiedlichste Branchen.
Materialeigenschaften & Auswahlkriterien
Das richtige Material zu wählen, ist entscheidend für Funktion und Kosten eines Bauteils. Jedes Material hat eigene Eigenschaften, die beeinflussen:
- Wie gut es sich bearbeiten lässt.
- Seine Festigkeit.
- Wie gut es vor Rost geschützt ist.
- Sein Gewicht und seine Kosten.
Einige Beispiele: Aluminium ist leicht zu bearbeiten, aber nicht so verschleißfest wie Stahl. Edelstahl ist sehr korrosionsbeständig, aber schwerer zu fräsen. Titan ist extrem fest und körperverträglich, aber auch sehr teuer.
Bei der Auswahl muss man die Anwendungsgebiete jeder Branche genau kennen:
- Luftfahrt: Hier sind Leichtigkeit und Festigkeit von Titan oder speziellen Aluminiumlegierungen entscheidend.
- Medizintechnik: Biokompatibilität und Genauigkeit bei Titan und bestimmten Kunststoffen sind wichtig.
- Automobilbau: Das Kosten-Nutzen-Verhältnis und die mechanischen Eigenschaften zählen.
Ein gutes Wissen über Materialien ist also unerlässlich, um die beste Lösung für jedes Projekt zu finden.
4. Fertigungsverfahren & Bearbeitungsmöglichkeiten
Fräsverfahren im Überblick
Die Art des Fräsverfahrens bestimmt, wie komplex und genau gefräste Teile werden können.
- 3-Achs-Fräsen:
- Die einfachste und häufigste Methode.
- Ideal für Teile mit flachen Oberflächen und einfachen Formen. Das Werkzeug bewegt sich in X-, Y- und Z-Richtung.
- 3+2-Achs-Fräsen:
- Für komplexere Formen.
- Das Werkstück oder der Fräskopf kann zusätzlich gedreht werden, um schwer erreichbare Stellen zu bearbeiten. Dabei bewegen sich immer noch drei Achsen gleichzeitig.
- 5-Achs-Fräsen:
- Das Werkzeug und/oder das Werkstück können sich auf fünf Achsen gleichzeitig bewegen.
- Perfekt für Freiformflächen und sehr komplexe Bauteile.
- Simultanfräsen:
- Die höchste Stufe des 5-Achs-Fräsens.
- Alle fünf Achsen bewegen sich durchgehend und gleichzeitig. Das sorgt für sehr glatte Übergänge und beste Oberflächen.
Jedes Verfahren hat Vorteile für bestimmte Formen und Genauigkeitsanforderungen.
Zusätzliche Bearbeitungen
Neben dem reinen Fräsen bieten moderne CNC-Maschinen viele weitere Bearbeitungsmöglichkeiten. So lassen sich komplexe Teile in einem Arbeitsgang herstellen. Das spart Rüstzeiten und Kosten.
Dazu gehört:
- Gewindeschneiden: Gewinde können direkt in der Maschine geschnitten werden, sowohl metrische als auch amerikanische Normen wie UNC und UNF.
- Planfräsen: Für ebene und genaue Oberflächen.
- Profilfräsen: Zum Erstellen spezieller Konturen und Formen.
Nach der mechanischen Bearbeitung sind oft Oberflächenveredelungen nötig. Sie verbessern die Funktion, das Aussehen oder den Rostschutz des Teils. Beispiele hierfür sind:
- Anodisieren von Aluminium: Erzeugt eine schützende und oft farbige Schicht.
- Pulverbeschichten: Bietet eine widerstandsfähige Oberfläche.
Diese zusätzlichen Schritte direkt in den Fertigungsprozess einzubinden, optimiert die Lieferkette und sichert höchste Qualität.
5. Anwendungsbereiche und Branchenlösungen
Branchen im Fokus
CNC-Fräsen ist eine Schlüsseltechnologie. Sie ist in vielen Hightech-Branchen unverzichtbar:
- Luftfahrt: Hier werden leichte, aber sehr starke Bauteile aus Aluminium oder Titan gefräst. Sie müssen extremen Belastungen standhalten.
- Medizintechnik: Für biokompatible Implantate, chirurgische Instrumente und Prothesen. Hier sind höchste Präzision und Oberflächengüte entscheidend.
- Automobilbau: Fertigung von Prototypen, komplexen Motorteilen, Formen für Karosserien und Serienteilen für Hochleistungsautos.
- Robotik: Präzise gefertigte Gelenke und Bauteile für Roboter und Automatisierungslösungen.
- Maschinenbau: Eine große Vielfalt an Komponenten, von Getriebeteilen über Gehäuse bis zu Werkzeugen, die wiederum andere Maschinen bauen.
Prototypenfertigung und Serienproduktion
Das CNC-Fräsen eignet sich hervorragend für die Prototypenfertigung und die Serienproduktion. Es bietet dabei klare Vorteile:
- Rapid Prototyping (schnelle Musterfertigung):
- Ermöglicht die schnelle und günstige Herstellung von funktionalen Prototypen aus dem echten Material.
- Ingenieure können ihre Entwürfe früh testen und verbessern. Das verkürzt die Entwicklungszeit.
- Kleinserien:
- Ideal, da keine teuren Werkzeuge oder Formen nötig sind.
- Die flexible Programmierung erlaubt schnelle Anpassungen und Varianten.
- Serienproduktion:
- Hier zeigen sich die Stärken des CNC-Fräsens in Bezug auf Präzision, Wiederholbarkeit und Effizienz.
- Automatisierte Abläufe garantieren gleichbleibende Qualität auch bei großen Stückzahlen.
Großbauteile-Fertigung
Die Herstellung großer Bauteile erfordert besondere Maschinen und Fachwissen. CNC-Fräsen ist hier die ideale Technologie. Unternehmen, die auf große Präzisionsteile spezialisiert sind – zum Beispiel bis zu 4 Meter lang oder 4 Tonnen schwer – nutzen modernste 5-Achs-Technologie und entsprechende Großmaschinen.
Diese riesigen Bearbeitungszentren können selbst sehr große und komplexe Teile in einem einzigen Arbeitsgang bearbeiten. Das verringert Fehler durch mehrfaches Umspannen, sichert höchste Präzision und spart viel Bearbeitungszeit.
Einsatzbereiche sind unter anderem:
- Luftfahrt (Flugzeugrümpfe)
- Energiesektor (Turbinenschaufeln)
- Schiffbau
Das Fachwissen in der Großbauteile-Fertigung bedeutet nicht nur die passenden Maschinen, sondern auch ein tiefes Verständnis für die Materialien und die beste Bearbeitungsstrategie bei diesen Größen.
6. Qualität, Sicherheit & Standards
ISO-Zertifizierungen und Qualitätsstandards
In der Fertigung sind Qualität und die Einhaltung strenger Standards extrem wichtig. ISO-Zertifizierungen sind international anerkannte Nachweise für gute Management- und Produktionsprozesse.
Wichtige Zertifizierungen sind:
- ISO 9001: Zeigt ein gutes Qualitätsmanagementsystem.
- ISO 14001: Bestätigt ein Umweltmanagementsystem.
- ISO 2768: Legt allgemeine Toleranzen für Maße und Formen fest (wichtig für technische Zeichnungen).
Zusätzliche Branchenzertifizierungen wie DNV (für die Marine- und Energiebranche) oder JOSCAR (für Verteidigung, Luft- und Raumfahrt sowie Sicherheit) zeigen, dass sehr hohe Branchennormen erfüllt werden. Diese Zertifikate sind ein wichtiges Gütesiegel und schaffen Vertrauen.
Geistiges Eigentum & Datenschutz
Der Schutz von geistigem Eigentum und Datenschutz ist in der digitalen Fertigung sehr wichtig. Kundendesigns und technische Daten sind oft streng geheim.
Seriöse Fertigungsdienstleister achten sehr auf die Vertraulichkeit der übermittelten Daten. Das wird durch strenge Regeln und technische Sicherheitsmaßnahmen sichergestellt. Der Abschluss von Non-Disclosure Agreements (NDAs), also Vertraulichkeitsvereinbarungen, ist hier Standard. Diese Verträge stellen sicher, dass Informationen nur für den vereinbarten Zweck genutzt werden.
Auch der Schutz vor unbefugtem Zugriff auf Kundendesigns ist wichtig. Dies geschieht durch sichere Server, verschlüsselte Datenübertragung und regelmäßige Sicherheitsprüfungen. Kunden können sich darauf verlassen, dass ihre Ideen sicher sind.
Qualitätssicherung & Messtechnik
Eine umfassende Qualitätssicherung ist das A und O beim Bau präziser CNC-Teile. Sie beginnt nicht erst am Ende, sondern begleitet den gesamten Herstellungsprozess.
Dabei ist der Einsatz modernster Messtechnik unerlässlich:
- Hochgenaue Koordinatenmessmaschinen (KMM).
- Optische Messsysteme und 3D-Scanner.
Prüfberichte mit genauen Messergebnissen dokumentieren, ob die vorgegebenen Toleranzen eingehalten wurden. Viele moderne CNC-Maschinen haben auch automatisierte Qualitätskontrollen. Dabei prüfen Messtaster direkt in der Maschine die Werkstücke und können gegebenenfalls Korrekturen vornehmen. Diese Kontrollen während der Fertigung minimieren Ausschuss und steigern die Effizienz. Das Ergebnis ist eine durchgängige und nachweisbare Qualität.
7. Kundenservice & Bestellprozesse
Bestellablauf und Online-Angebotsysteme
Ein einfacher Bestellablauf ist für Kunden in der CNC-Fertigung sehr wichtig. Viele moderne Anbieter nutzen dazu praktische Online-Angebotsysteme.
Der Ablauf sieht oft so aus:
- Zeichnungs-Upload: Kunden laden ihre CAD-Modelle oder technischen Zeichnungen hoch.
- Angebotserstellung: Das System analysiert die Daten und erstellt schnell ein detailliertes Angebot mit Preisen und Lieferzeiten.
- Produktionsüberwachung: Über ein Kundenportal können Kunden den Status ihres Auftrags verfolgen.
- Termingerechte Lieferung: Eine effiziente Logistik sorgt dafür, dass die Teile pünktlich ankommen.
Diese digitalen Prozesse sparen Zeit, reduzieren den Papierkram und sorgen für hohe Effizienz.
Kunden-Support & Ressourcen
Ein guter Kunden-Support bedeutet mehr als nur Aufträge bearbeiten. Er bietet umfassende Ressourcen für die Kunden. Dazu gehören:
- Detaillierte Leitfäden und Videos: Erklären den Bestellprozess, geben Tipps zur Konstruktion oder beantworten Fragen.
- Umfassende FAQs (Häufig gestellte Fragen): Behandeln die meisten Anliegen.
- Persönliche Beratung: Für spezielle oder schwierige Fragen durch erfahrene Fachleute.
- Feste Ansprechpartner: Sorgen dafür, dass Kunden bei wiederholten Aufträgen immer denselben kompetenten Kontakt haben.
Dieser Service schafft Vertrauen und ermöglicht eine reibungslose Zusammenarbeit.
Lieferzeiten & Flexibilität
In der heutigen schnellen Fertigung sind Lieferzeiten und Flexibilität entscheidend. Viele Anbieter bieten daher verschiedene Optionen an:
- Standard-Fertigung: Ideal, wenn es nicht super eilig ist. Dies ist meist die günstigste Lösung.
- Expressfertigung: Für sehr dringende Projekte. Hier wird die Bearbeitung beschleunigt, was aber etwas mehr kostet.
Ein gutes Lieferkettenmanagement ist wichtig. Es hilft, Material und Produktionskapazitäten optimal zu planen. Die Fähigkeit, schnell auf neue Kundenanforderungen zu reagieren, zeigt, wie kundenorientiert und verlässlich ein Fertigungsdienstleister ist.
8. Wirtschaftlichkeit & Effizienz
Vorteile von CNC-Fräsen für Unternehmen
Das CNC-Fräsen bringt Unternehmen viele Vorteile. Diese wirken sich direkt auf die Wirtschaftlichkeit und Wettbewerbsfähigkeit aus:
- Präzision: Minimiert fehlerhafte Teile und sichert gleichbleibend hohe Qualität. Das reduziert Reklamationen.
- Materialeffizienz: Durch kluge Frässtrategien und optimiertes Materiallayout wird weniger Rohmaterial verbraucht. Das spart besonders bei teuren Materialien erhebliche Kosten.
- Reduzierte Personalkosten: Hohe Automatisierung verringert den Bedarf an Handarbeit. Das führt zu geringeren Personalkosten und höherer Produktivität pro Mitarbeiter.
Diese Kombination aus Genauigkeit, Materialeffizienz und Kosteneinsparungen macht CNC-Fräsen zu einer langfristig lohnenden Investition.
Effizienzsteigerung durch Automatisierung
Weit fortgeschrittene Automatisierung ist der Schlüssel zu mehr Effizienz beim CNC-Fräsen.
Wichtige Punkte der Automatisierung:
- Kürzere Rüstzeiten: Automatische Werkzeugwechsler und Palettenwechselsysteme minimieren Stillstandzeiten.
- Weniger Ausschuss: Menschliche Fehler werden ausgeschlossen, und die genaue Steuerung sichert eine gleichbleibende Qualität über die ganze Serie.
- Integration mehrerer Prozesse: Fräsen, Bohren und Gewindeschneiden können in einem Arbeitsgang erledigt werden. Das spart Transport- und Einrichtungszeit.
Diese umfassende Automatisierung steigert die Produktivität enorm und senkt die Fertigungskosten pro Teil.
Rahmenverträge & Langfristige Partnerschaften
Für Unternehmen, die regelmäßig bestimmte Bauteile brauchen, sind Rahmenverträge und langfristige Partnerschaften mit CNC-Fertigungsdienstleistern sehr vorteilhaft.
Ein Rahmenvertrag sichert nicht nur die Verfügbarkeit der Teile, sondern auch eine Preisstabilität über längere Zeit. Das hilft bei der Kostenplanung und schützt vor Preisschwankungen. Für die Sicherheit in der Serienfertigung sind solche Partnerschaften unerlässlich, da sie eine verlässliche und pünktliche Lieferung großer Mengen garantieren.
Solche Partnerschaften basieren auf Vertrauen und Verständnis. Sie ermöglichen eine engere Zusammenarbeit bei der Produktentwicklung und Prozessoptimierung. Das führt zu höherer Qualität, Kosteneffizienz und einer starken Position im Wettbewerb für beide Seiten.
9. Historisches & Marktüberblick
Historischer Hintergrund der CNC-Technologie
Die Entwicklung der CNC-Technologie ist eine spannende Reise von mechanischen zu digitalen Steuerungssystemen, die die Fertigungsindustrie grundlegend verändert hat.
- Anfänge in den 1940ern: Begann mit der Numerischen Steuerung (NC) am MIT. Programme wurden damals über Lochkarten oder Magnetbänder in die Maschinen eingegeben.
- Wandel in den 1970ern: Der Übergang zur Computerized Numerical Control (CNC). Mit Mikroprozessoren wurden die Steuerungen viel leistungsfähiger, kleiner und flexibler. Software ersetzte die alten Datenträger, was die Programmierung einfacher machte.
Seitdem hat sich die Technik ständig verbessert. Heute gibt es hochkomplexe 5-Achs-Systeme und umfassende Automatisierung, die die digitale Fertigung prägen.
Führende Hersteller von CNC-Steuerungen
Der Markt für CNC-Steuerungen wird von einigen großen Firmen weltweit beherrscht. Sie unterscheiden sich durch ihre Innovationen und Leistungsmerkmale.
- Fanuc (Japan): Einer der weltweit führenden Hersteller. Bekannt für sehr robuste, zuverlässige und einfach zu bedienende Steuerungen. Sie sind weit verbreitet und gut standardisiert.
- Siemens (Deutschland): Ihre SINUMERIK-Steuerungen sind für fortschrittliche Funktionen, hohe Flexibilität und gute Vernetzungsmöglichkeiten bekannt. Besonders stark in komplexen und vollautomatisierten Fertigungen.
- Heidenhain (Deutschland): Spezialisiert auf sehr genaue Messsysteme und Steuerungen. Sie bieten höchste Präzision und eine einfache Bedienung, besonders im Bereich der 5-Achs-Bearbeitung.
Jede dieser Marken hat ihren eigenen Platz im Markt. Sie alle tragen aber maßgeblich dazu bei, die CNC-Technologie weiterzuentwickeln und effizientere Lösungen für die digitale Fertigung zu bieten.
TÜV zertifizierte CNC Lohnfertigung nach ISO 9001
Wir erfüllen höchste Standards in der Fertigung durch unser Qualitätsmanagement nach ISO 9001:2015 und Umweltmanagement nach ISO 14001:2015. Mit regelmäßigen Qualitätskontrollen und präziser Werkstoffprüfung stellen wir sicher, dass jedes Werkstück maßgenau ist. Durch dokumentierte Prozesse und kontinuierliche Kontrollen garantieren wir eine lückenlose Rückverfolgbarkeit und gleichbleibende Präzision.
Kontakt
Kontaktieren Sie uns für präzise Lösungen in der Zerspanungstechnik. Wir freuen uns auf Ihre Anfrage.
Büro / Fertigungsstätte
Unser Standort in Solingen – hier sind wir für Sie erreichbar. Besuchen Sie uns gerne persönlich.
Telefon
Rufen Sie uns an, um ein unverbindliches Beratungsgespräch zu vereinbaren. Wir freuen uns auf Ihren Anruf!
Kontaktieren Sie uns per E-Mail für weitere Informationen oder um eine Anfrage zu senden. Wir melden uns schnellstmöglich bei Ihnen.